Why Is My DTF Transfers Not Sticking to My Shirt?
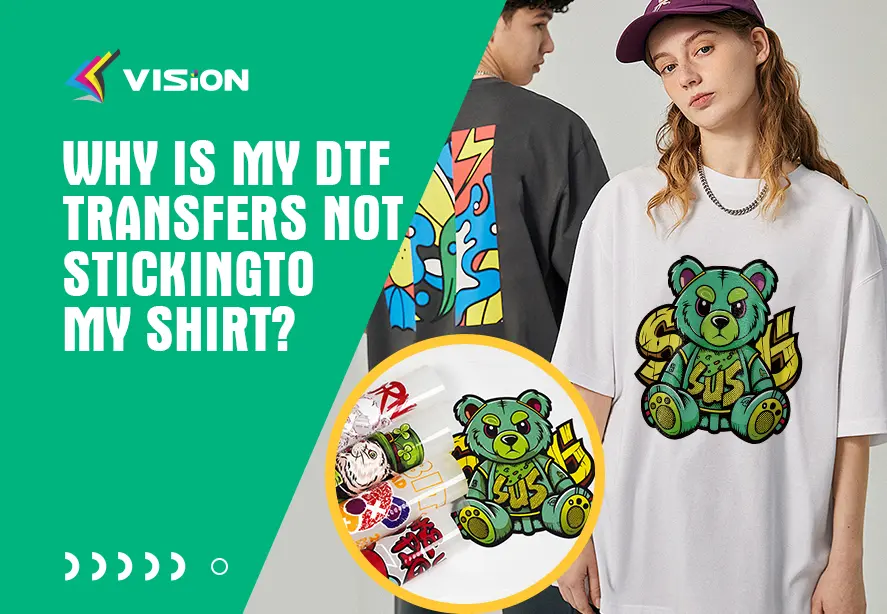
Direct-to-Film (DTF) printing has gained immense popularity due to its versatility, vibrant colors, and ability to adhere to various fabrics. However, one of the most common issues faced by users is DTF transfers not sticking properly to the fabric. If you are experiencing problems with DTF prints peeling off, not adhering correctly, or washing away too soon, this comprehensive guide will help you troubleshoot and fix the issue.
Common Reasons Why DTF Transfers Fail to Stick
There are several factors that can lead to DTF transfer failures. Let’s go through each one in detail.
Incorrect Heat Press Settings
Applying the right temperature, pressure, and time is crucial for a successful DTF transfer. If any of these parameters are incorrect, the transfer may not adhere properly.
Temperature: The recommended temperature for DTF transfers is typically 310°F to 329°F (155°C to 165°C). Too low, and the adhesive won’t activate; too high, and the design may burn or lose vibrancy.
Pressure: Medium to firm pressure is required to ensure the transfer fully adheres to the fabric.
Time: Pressing for about 10 to 15 seconds ensures proper adhesion. Under-pressing or over-pressing can cause peeling issues.
Poor Quality DTF Film or Ink
Not all DTF films and inks are created equal. Low-quality materials can result in poor adhesion.
DTF Film: Make sure you are using a premium matte or cold-peel film with proper adhesion properties.
DTF Ink: Use high-quality, pigment-based DTF inks designed for elasticity and durability.
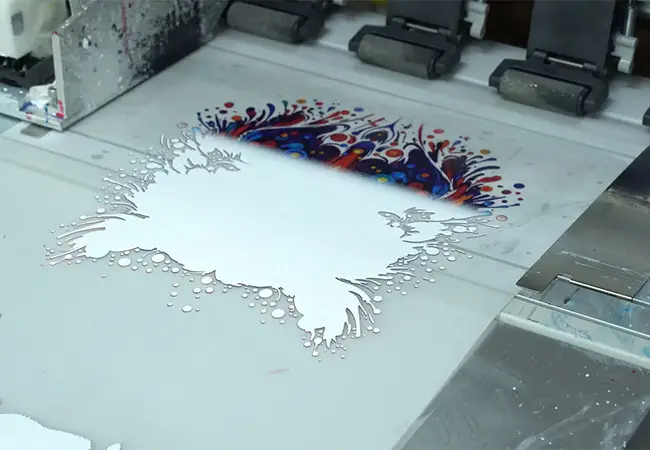
dtf film printing
Humidity and Moisture Issues
Excessive humidity can affect the curing process of DTF powder and lead to poor adhesion. Ensure your workspace is dry and store your DTF prints in a moisture-free environment.
Improper Powder Application
DTF powder acts as an adhesive, bonding the ink to the fabric. If the powder is not applied evenly or not cured properly, adhesion problems can occur.
Make sure the powder is evenly coated over the design.
The curing process should be at 320°F (160°C) for 2-3 minutes until it melts and turns glossy.
Fabric Type and Treatment
Not all fabrics work equally well with DTF. Some synthetic fabrics contain coatings that resist heat transfer adhesion. Always ensure:
The fabric is cotton, polyester, or a blend suitable for DTF printing.
The fabric is clean and pre-pressed to remove moisture and wrinkles.
A pre-treatment solution is used if necessary for difficult fabrics.
Peeling Method and Timing
Peeling the film incorrectly can lead to adhesion issues.
Cold Peel vs. Hot Peel: Some DTF films require cold peeling (waiting for it to cool completely), while others allow hot peeling. Check manufacturer guidelines.
Peeling Angle: Peel the film at a smooth, steady angle to avoid lifting.
How to Fix DTF Transfers Not Sticking to Shirts
Now that we’ve identified the possible causes, let’s discuss step-by-step solutions to fix DTF transfer adhesion issues.
Adjust Your Heat Press Settings
To ensure proper adhesion, check and calibrate your heat press:
Increase or decrease the temperature slightly within the 310°F-329°F range and test again.
Apply medium to firm pressure to ensure complete contact.
Press for 10-15 seconds, and if peeling still occurs, try pressing for a few more seconds.
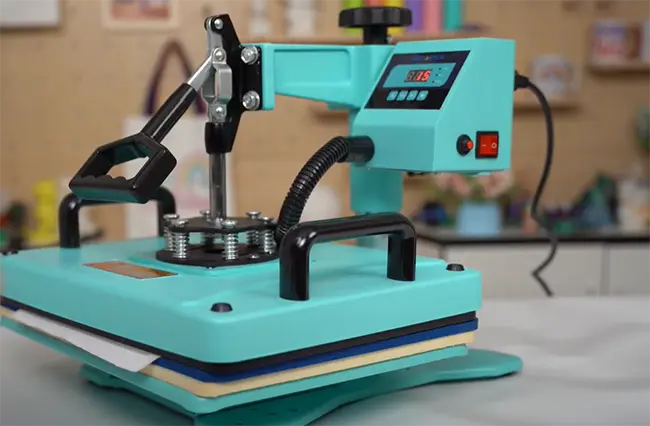
heat pressing
Use High-Quality DTF Supplies
Invest in reliable DTF films, inks, and powders. Inferior products lead to poor adhesion and fading.
Choose branded DTF inks with a proven track record.
Always purchase high-quality cold peel or hot peel films.
Proper Curing of the DTF Powder
Improper curing can lead to weak adhesion. Follow these guidelines:
Set your curing oven or heat gun to 320°F (160°C).
Heat until the powder turns glossy and fully melts.
Do not overheat, as this can cause the adhesive to burn and lose effectiveness.
Improve Work Environment Conditions
Moisture and humidity impact DTF transfer success. Ensure:
Your workspace has a humidity level of around 40-50%.
Prints are stored in a dry, sealed container before pressing.
Fabric is pre-pressed for 3-5 seconds to remove any moisture.
Test Different Fabrics
If your DTF transfers are not sticking, the issue might be the fabric type. Try these solutions:
Use cotton, polyester, or cotton-poly blends.
For synthetic materials like nylon, use a DTF-specific pre-treatment.
Troubleshooting Peeling and Lifting Issues After Pressing
Even after pressing correctly, you may experience peeling or lifting of the design. Here’s how to fix it:
Hot Peel vs. Cold Peel Issues
If you’re using a hot peel film, peel it immediately after pressing. If using a cold peel film, wait for it to cool completely before peeling.
Repressing the Design
If peeling occurs:
Place parchment paper or a Teflon sheet over the design.
Repress at the same temperature for 5-7 seconds to ensure full adhesion.
Washing and Maintenance Tips
To improve durability, follow these care tips:
Wash garments inside out in cold water.
Avoid high heat drying—air drying is best.
Do not use bleach or harsh detergents.
Ensuring a successful DTF transfer requires careful attention to heat settings, materials, and application techniques. By following the troubleshooting tips in this guide, you can prevent peeling, poor adhesion, and transfer failures.
If you’re still experiencing issues, try testing with different heat press settings, high-quality supplies, and proper curing techniques. With the right adjustments, you’ll achieve vibrant, durable DTF prints that last wash after wash.
Related:
Why Are My DTF Prints Wrinkling After Washing?
Top Tips for Vibrant Colors in DTF Printing
Do you need special ink for DTF transfers?
Why Is My DTF Powder Not Sticking to the Film?
Why is my DTF transfer cracking?
Unveiling High-Quality DTF Film
DTF powder for printing