Why does paper structure affect the ink absorption performance of sublimation paper?
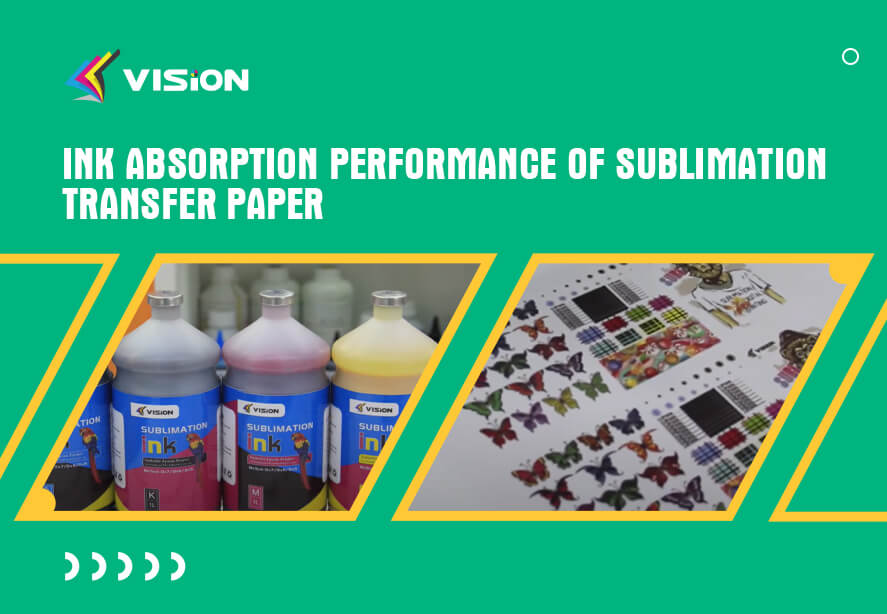
The structure of sublimation transfer paper plays a crucial role in determining its ink absorption performance. Understanding why paper structure affects ink absorption is essential for achieving optimal printing results in sublimation transfer processes. In this article, we will explore the relationship between paper structure and ink absorption performance, as well as the factors that influence this interaction.
Importance of Ink Absorption in Sublimation Transfer Paper
Sublimation transfer paper is specifically designed for dye-sublimation printing, a process where heat and pressure are used to transfer ink onto various substrates, such as polyester fabrics and coated ceramics. Ink absorption is a critical factor in this process, as it directly impacts the color vibrancy, sharpness, and durability of the printed image.
Efficient ink absorption ensures that the ink is quickly and uniformly absorbed by the paper, preventing smudging, bleeding, or uneven color distribution. It also allows for better control over dot gain, which refers to the increase in the size of printed dots compared to their original size. A well-absorbing paper can effectively limit dot gain, resulting in sharper and more accurate prints.
Influence of Paper Structure on Ink Absorption Performance
The structure of sublimation transfer paper influences its ink absorption performance through various factors, including porosity, surface smoothness, and coating characteristics.
Porosity
Porosity refers to the openness or permeability of the paper structure. A more porous paper allows ink to penetrate and spread throughout the fibers, facilitating better absorption. When ink is efficiently absorbed, it minimizes the risk of pooling or smudging on the paper surface. On the other hand, a less porous paper may hinder ink absorption, leading to slower drying times and potential image quality issues.
Surface Smoothness
The smoothness of the paper surface also affects ink absorption. A smooth surface provides a more even and controlled ink flow, allowing for better color saturation and sharper image reproduction. In contrast, a rough or uneven surface can disrupt the ink flow, leading to inconsistent absorption and potential print defects.
Coating Characteristics
Many sublimation transfer papers have a specialized coating on their surface. This coating is designed to enhance ink absorption and retention, as well as to prevent ink bleeding or feathering. The thickness and composition of the coating impact the paper’s ability to absorb ink. An optimized coating formulation ensures that the ink is quickly absorbed, stays in place, and produces vibrant and durable prints.
VISION sublimation paper factory
Factors Affecting Paper Structure and Ink Absorption Performance
Several factors influence the structure of sublimation transfer paper and, consequently, its ink absorption performance. These factors include:
Fiber Composition
The type of fibers used in the paper manufacturing process can affect its structure and porosity. For sublimation transfer paper, polyester fibers are commonly used due to their high affinity for sublimation inks. Polyester fibers provide excellent ink absorption properties, allowing for vibrant and long-lasting prints.
Paper Weight and Thickness
The weight and thickness of the paper also impact its structure and ink absorption performance. Heavier papers typically have a denser structure, which may affect ink penetration and absorption. However, excessively thin papers can be prone to ink bleeding or show-through on the substrate. Finding the right balance of weight and thickness is crucial for achieving optimal ink absorption.
Coating Formulation
As mentioned earlier, the coating applied to the paper surface significantly influences ink absorption. The formulation of the coating, including its composition and thickness, is carefully designed to ensure proper ink absorption and retention. Different paper manufacturers may use variations in coating formulation, resulting in variations in ink absorption performance.
Surface Treatment
Surface treatment processes, such as calendaring or sizing, can also impact the paper structure and surface smoothness. Calendaring involves compressing the paper between metal rollers to create a smoother surface, while sizing adds a protective film to enhance ink absorption. These treatments can improve the paper’s ink absorption performance and overall print quality.
The structure of sublimation transfer paper plays a vital role in its ink absorption performance. Factors such as porosity, surface smoothness, coating characteristics, fiber composition, paper weight, and surface treatment all contribute to how effectively the paper absorbs ink. By understanding the relationship between paper structure and ink absorption, digital printers can select the most suitable sublimation transfer paper for achieving high-quality, vibrant, and durable prints.
How to Optimize Ink Absorption of Sublimation Transfer Paper?
To ensure optimal ink absorption in sublimation transfer paper, several strategies can be implemented:
Paper Selection
Choosing the right type of sublimation transfer paper is crucial for achieving desired ink absorption performance. Different papers have varying characteristics, such as porosity, coating formulation, and surface smoothness. Conducting research, reading product specifications, and testing different papers can help identify the most suitable option for specific printing requirements.
Coating Thickness Adjustment
The thickness of the coating applied to sublimation transfer paper can be adjusted to optimize ink absorption. Thicker coatings can enhance ink absorption and retention, resulting in more vibrant and durable prints. However, excessively thick coatings may impede ink drying and lead to longer production times. Finding the right balance is essential for achieving optimal results.
Surface Treatment Modification
Modifying the surface treatment processes, such as adjusting the calendaring pressure or altering the sizing formulation, can impact the paper’s structure and surface smoothness. Fine-tuning these treatments can improve ink absorption performance and overall print quality. It may require collaboration with paper manufacturers or conducting internal experiments to identify the most effective modifications.
Pre-Printing Preparation
Proper pre-printing preparation is essential for optimizing ink absorption. This includes ensuring the sublimation transfer paper is clean, free from moisture, and stored in a suitable environment. Contaminants or moisture on the paper can affect ink absorption and result in poor print quality. Storing the paper in a controlled environment with moderate humidity levels can help maintain its optimal ink absorption properties.
Print Settings Adjustment
In addition to paper-related factors, adjusting print settings can also impact ink absorption. Variables such as ink density, print speed, and heat press temperature can affect how the ink interacts with the paper. Experimenting with different settings and conducting test prints can help determine the ideal combination for achieving optimal ink absorption and vibrant prints.
The structure of sublimation transfer paper significantly influences its ink absorption performance. Factors such as paper selection, coating thickness adjustment, surface treatment modification, pre-printing preparation, and print settings adjustment all contribute to optimizing ink absorption. By understanding these factors and implementing appropriate strategies, digital printers can achieve high-quality prints with vibrant colors, sharp details, and excellent durability.
Related:
What sublimation paper is and its role in the sublimation printing process