Why Are My DTF Prints Wrinkling After Washing?
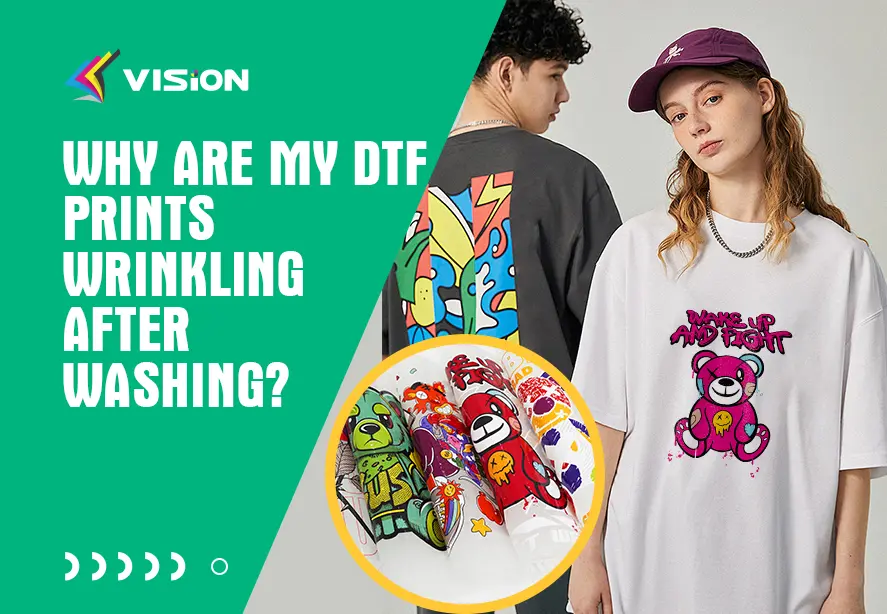
When it comes to Direct-to-Film (DTF) printing, achieving durable, wash-resistant prints is essential for customer satisfaction and business reputation. If you’re experiencing wrinkling in your DTF prints after washing, you’re facing a common but solvable problem. In this comprehensive guide, we’ll explore the causes of DTF print wrinkling and provide actionable solutions to ensure your prints maintain their quality through multiple wash cycles.
Common Causes of Wrinkling in DTF Prints
1.Improper Application Techniques
One of the primary reasons DTF prints wrinkle after washing is improper application during the initial printing and heat pressing process. When the adhesive powder isn’t properly melted or the heat press settings aren’t optimized, the print doesn’t properly bond with the fabric, leading to wrinkling after washing.
2.Inadequate Curing Time and Temperature
DTF prints require specific temperature and time settings to properly cure. Insufficient heat or pressing time can result in an incomplete bond between the print and fabric, making the print susceptible to wrinkling when exposed to water and agitation during washing.
3. Poor Film and Powder Quality
The quality of your DTF film and adhesive powder plays a significant role. Low-quality materials may not adhere well, leading to print distortions. Using high-grade consumables ensures durability and flexibility, reducing the risk of wrinkles after washing.
4. Incorrect Washing Methods
Washing printed garments in hot water or using harsh detergents can weaken the adhesive. This leads to shrinkage and wrinkling. To extend print life, wash in cold water with mild detergent and turn garments inside out before washing.
5. Fabric Compatibility Issues
Not all fabrics react the same way to DTF prints. Materials that shrink significantly during washing can cause the print to wrinkle. Using fabrics with minimal shrinkage, such as pre-shrunk cotton, can help maintain print integrity.
How to Prevent DTF Prints Wrinkling
1. Optimizing Your Heat Press Settings
To prevent wrinkling, we recommend:
- Temperature Calibration: Ensure your heat press is accurately calibrated to reach the recommended temperature (typically 320-330°For 160-165°C for most DTF applications).
- Proper Pressure: Apply medium to firm pressure during heat pressing to ensure the adhesive fully bonds with the fabric.
- Adequate Pressing Time: Press for the recommended duration (usually 15-20 seconds) to allow the adhesive to fully melt and bond with the garment.
2.Two-Stage Pressing Technique
For superior results, implement a two-stage pressing process:
- Initial Press: Apply the first press to melt the adhesive powder and create the initial bond.
- Cool Down Period: Allow the print to cool slightly (10-15 seconds).
- Second Press: Apply a second press to further secure the bond and enhance durability.
heat pressing
3.Proper Pre and Post-Treatment of Garments
- Pre-Press Garments: Before applying the DTF transfer, pre-press the garment for 5-10 seconds to remove moisture and create a smooth surface.
- Post-Press Care: After heat pressing, allow the garment to cool completely before handling or packaging.
- Washing Instructions: Provide clear washing instructions to customers, recommending inside-out washing in cold water and air drying for maximum print longevity.
Advanced Troubleshooting for Persistent Wrinkling Issues
Evaluating Your DTF Powder Application
The adhesive powder layer plays a crucial role in print durability:
- Even Distribution: Ensure the adhesive powder is evenly distributed across the entire print area.
- Appropriate Amount: Apply sufficient powder to create a strong bond without excess that could cause cracking or flaking.
- Quality Control: Regularly check your powder application system for clogs or uneven distribution.
Fabric Compatibility Considerations
Not all fabrics respond the same way to DTF printing:
- Fabric Testing: Test your DTF prints on different fabric types to understand how each responds to washing.
- Fabric-Specific Settings: Adjust your heat press settings based on the specific fabric being printed (cotton, polyester, blends, etc.).
- Stretch Fabrics: For highly elastic fabrics, consider using specialized DTF adhesives designed for stretch materials.
Related:
Choosing the Best Fabric for DTF Printing
Professional Maintenance Tips for DTF Equipment
Regular maintenance of your DTF printing equipment can prevent many quality issues:
- Regular Calibration: Calibrate your heat press regularly to ensure accurate temperature readings.
- Clean Application Systems: Keep the powder shaker and application systems clean and free of clumps.
- Quality Control Checks: Implement a quality control process that includes wash testing sample prints before large production runs.
powder shaker
When to Consider Professional Assistance
If you’ve implemented all the above solutions and still experience wrinkling issues:
- Consult Suppliers: Reach out to your DTF film and powder suppliers for technical support.
- Professional Training: Consider investing in professional training to perfect your DTF application techniques.
- Equipment Upgrades: Evaluate whether your current equipment meets the requirements for professional DTF printing.
Wrinkling in DTF prints after washing is a common challenge that can be overcome with proper techniques, quality materials, and attention to detail. By optimizing your heat press settings, implementing a two-stage pressing process, and maintaining your equipment, you can produce DTF prints that maintain their quality and appearance through numerous wash cycles.
Related:
Why Is My DTF Powder Not Sticking to the Film?
What machine do you need for DTF printing?
Why is my DTF transfer cracking?
Troubleshooting Common DTF Printing Issues