The Ultimate Guide to DTF Printing
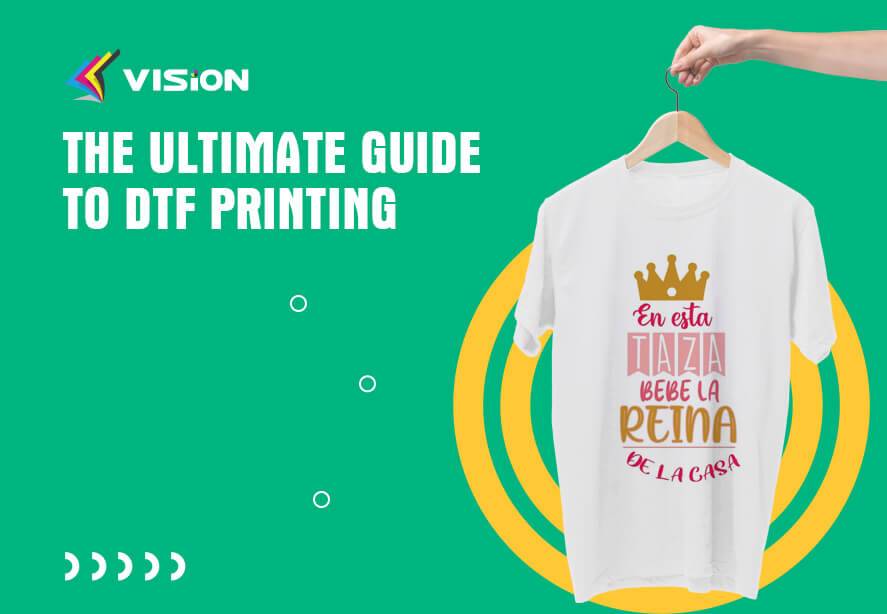
Table of Contents
- Introduction
- Benefits of DTF Printing
- Getting Started with DTF Printing
- Step-by-Step DTF Printing Process
- Troubleshooting and Tips for Successful DTF Printing
- DTF Printing vs. Other Printing Methods
- FAQs
Introduction
DTF printing is an innovative and increasingly popular method of printing that offers versatility and vibrant results. In this guide, we will explore the world of DTF printing, explaining its process, benefits, and how it differs from other printing methods. Whether you’re a printing enthusiast or a business owner looking to expand your printing capabilities, this comprehensive overview will provide you with the knowledge you need to get started with DTF printing.
If you’re looking to explore this exciting printing technique, Visionsub is the leading provider in the industry. With their expertise and state-of-the-art equipment, they offer the ultimate guide to DTF printing, covering everything from prepping your artwork to the printing process and post-processing techniques. Whether you’re a seasoned professional or just starting in the world of printing, Vision Sub’s comprehensive guide will help you unleash your creativity and achieve outstanding results. Don’t miss the opportunity to learn from the best in the field and take your DTF printing to new heights.
What is DTF Printing?
DTF stands for “Direct to Film,” a printing technique that involves transferring ink directly onto the fabric using a special DTF film. Unlike other methods that require a transfer medium, DTF printing eliminates the need for additional layers, resulting in a more efficient and cost-effective process.
Why is DTF Printing Gaining Popularity?
DTF printing has gained significant popularity in recent years due to its numerous advantages over traditional printing methods. It offers exceptional color vibrancy, the ability to print intricate designs, and the versatility to print on various fabrics, including cotton, polyester, and blends. Additionally, DTF printing is compatible with both light and dark-colored fabrics, expanding the possibilities for personalized and custom designs.
How DTF Printing Differs from Other Printing Methods
DTF printing sets itself apart from other printing methods through its unique process and materials. Unlike screen printing, which requires the creation of stencils, or DTG printing, which uses a digital printer, DTF printing transfers ink directly onto the fabric. This direct transfer method ensures sharper details and vivid colors, giving your prints a professional and eye-catching appearance.
Benefits of DTF Printing
DTF printing offers a range of benefits that make it an appealing choice for both individuals and businesses:
Versatility: DTF printing can be applied to various fabrics, including t-shirts, hoodies, hats, and more, allowing for a wide range of custom printing possibilities.
Vibrant Colors: The direct transfer of ink ensures exceptional color vibrancy, making your designs stand out with vivid and eye-catching hues.
High Detail: DTF printing enables the reproduction of intricate and complex designs with precise details, giving your prints a professional and sophisticated look.
Durability: The cured prints from DTF printing are highly durable and can withstand multiple washes without fading or cracking, ensuring long-lasting quality.
Cost-Effective: With DTF printing, you can create custom prints in small quantities without the need for expensive setup costs or minimum order requirements, making it an affordable option for personalized items.
Understanding DTF Printing
To get started with DTF printing, it’s essential to have a solid understanding of the process, materials, and equipment involved.
Explaining the DTF Printing Process
The DTF printing process involves several key steps:
Preparation: Prepare your artwork by converting it into a printable format and ensuring it meets the necessary resolution and color requirements.
Film Printing: Print the design onto a specialized DTF film using a compatible inkjet printer. The film acts as a carrier for the ink, which will later be transferred to the fabric.
Pre-Treatment: Apply a pre-treatment solution to the fabric to enhance ink adhesion and ensure vibrant and durable prints.
Adhesive Application: Coat the fabric with DTF powder (heat-activated adhesive) using a heat press or a Powder Shaker and Dryer. The adhesive provides a bonding layer between the fabric and the ink.
Transfer: Place the DTF film onto the fabric, aligning it with the desired print area. Apply heat and pressure using a heat press to transfer the ink from the film to the fabric.
Curing: After the transfer, cure the print using a heat press or a curing machine to ensure the ink adheres firmly to the fabric and achieves maximum durability.
Materials and Equipment Required for DTF Printing
To embark on your DTF printing journey, you’ll need the following materials and equipment:
DTF Printer: An inkjet printer specifically designed for DTF printing, capable of printing onto the DTF film accurately.
DTF Films: Specialized films that act as carriers for the ink. These films are compatible with DTF printers and can withstand the transfer process.
Pre-Treatment Solution: A solution that prepares the fabric for printing by enhancing ink adhesion and color vibrancy. Choose a pre-treatment solution suitable for the fabric type you’re using.
Heat Press: A heat press machine is used to apply heat and pressure during the transfer process, ensuring proper ink bonding and curing.
Powder Shaker and Dryer Machine: Alternatively, you can use a DTF Powder Shaker and Dryer to apply the powder (heat-activated adhesive) to the fabric before the transfer.
Pros and Cons of DTF Printing Compared to Other Methods
Before diving into DTF printing, it’s important to consider its pros and cons in relation to other popular printing methods:
Pros of DTF Printing:
Excellent color vibrancy and print quality
Ability to print on various fabric types and colors
Suitable for both small and large print runs
High level of detail and sharpness
Durability and resistance to fading or cracking
Cons of DTF Printing:
Initial investment in specialized equipment
Longer processing time compared to other methods
Requires additional steps for pre-treatment and adhesive application
In the next section, we’ll explore the step-by-step process of DTF printing, ensuring you have a comprehensive understanding of each stage.
Getting Started with DTF Printing
To achieve successful DTF prints, it’s crucial to follow the correct procedures for artwork preparation, fabric selection, and color limitations.
Preparing Your Artwork for DTF Printing
Before printing your design, ensure that it meets the following requirements:
Resolution: Set your artwork resolution to a minimum of 300 DPI (dots per inch) to ensure sharp and high-quality prints.
Color Mode: Use the CMYK color mode for your artwork to ensure accurate color representation during the printing process.
File Format: Save your artwork in a compatible file format, such as PNG or TIFF, to preserve transparency and image quality.
Choosing the Right Fabric for DTF Printing
DTF printing is compatible with various fabric types, including cotton, polyester, and blends. Consider the following factors when selecting fabric for your DTF prints:
Fabric Composition: Ensure that the fabric composition is suitable for DTF printing. Fabrics with higher polyester content tend to yield better results.
Fabric Color: DTF printing works well on both light and dark-colored fabrics. However, keep in mind that dark-colored fabrics may require an additional layer of white ink to enhance color vibrancy.
Fabric Texture: Smooth and flat fabrics generally produce the best DTF prints. Fabrics with a rough texture or heavy texture may result in reduced print quality.
Understanding the Color Limitations in DTF Printing
DTF printing offers vibrant color reproduction but has certain limitations to consider:
Color Gamut: DTF printing has a wide color gamut, allowing for accurate color representation. However, certain colors, such as neon or metallic shades, may not be achievable through DTF printing alone.
White Ink: When printing on dark-colored fabrics, a layer of white ink is often necessary to ensure vibrant colors. This additional layer adds depth and brightness to the design.
By understanding these considerations, you can maximize the quality and visual impact of your DTF prints.
Step-by-Step DTF Printing Process
Now let’s dive into the step-by-step process of DTF printing, ensuring you have a comprehensive understanding of each stage.
Pre-Treatment of the Fabric
Pre-treat the fabric by applying a pre-treatment solution using a sprayer or a dedicated pre-treatment machine.
Ensure that the pre-treatment solution is evenly distributed and covers the entire printing area.
Allow the fabric to dry completely before proceeding to the next step.
Coating the Fabric with Adhesive
Place the pre-treated fabric on a heat press or a Powder Shaker and Dryer machine.
Apply the heat-activated adhesive powder evenly onto the fabric surface.
Use the recommended temperature and pressure settings for the adhesive application.
Ensure that the adhesive is evenly spread and covers the entire printing area.
Printing the Design onto the Fabric
Print your design onto the DTF film using a compatible inkjet printer.
Trim the film to match the size of your design and remove any excess film.
Place the DTF film with the printed side facing down onto the adhesive-coated fabric.
Use a heat press to apply heat and pressure, allowing the ink to transfer from the film to the fabric.
Follow the recommended temperature and pressing time for optimal results.
Once the transfer process is complete, carefully peel off the DTF film to reveal your printed design on the fabric.
Curing the Print for Durability
After the transfer, place the printed fabric onto the heat press for curing.
Set the temperature and pressing time according to the manufacturer’s recommendations for the specific ink and fabric used.
Apply heat and pressure to ensure proper curing and bonding of the ink onto the fabric.
Once the curing process is complete, allow the fabric to cool down before handling or washing.
Troubleshooting and Tips for Successful DTF Printing
Even with the right techniques, you may encounter some issues during the DTF printing process. Here are common problems and their solutions:
Common Issues Faced in DTF Printing and Their Solutions
Ink Bleeding: If the colors bleed or smudge during the transfer process, ensure that the film is properly aligned with the fabric, and adjust the heat press settings to achieve better ink bonding.
Uneven Prints: Uneven prints may occur due to inadequate adhesive application or uneven pressure during the transfer. Ensure that the adhesive is evenly spread, and apply consistent pressure using a heat press.
Poor Wash Fastness: If the prints fade or crack after washing, double-check the curing process. Adjust the temperature and pressing time to achieve proper ink adhesion and durability.
Tips for Achieving High-Quality Prints
Use high-resolution artwork to ensure sharp and detailed prints.
Perform test prints on sample fabrics before proceeding with larger production runs.
Follow the guidelines of DTF printing manufacturer for pre-treatment solution, adhesive, and ink compatibility.
Maintain your DTF printing equipment regularly to ensure optimal performance and longevity.
Proper Maintenance of DTF Printing Equipment
To keep your DTF printing equipment in good working condition, follow these maintenance tips:
Clean the inkjet printer regularly to prevent clogging and ensure consistent ink flow.
Regularly inspect and clean the heat press to remove any residual adhesive or ink.
Store the DTF films in a cool and dry place to prevent damage or degradation.
By following these troubleshooting tips and maintenance guidelines, you can overcome challenges and achieve successful DTF prints consistently.
DTF Printing vs Other Printing Methods
To better understand the advantages of DTF printing, let’s compare it to other popular printing methods:
Comparison with DTG Printing
DTF printing offers a wider color gamut and sharper details compared to DTG printing.
DTF printing can achieve vibrant prints on both light and dark-colored fabrics, whereas DTG printing may require additional steps or pre-treatment for dark-colored fabrics.
DTG printing is generally more suitable for small print runs, while DTF printing can accommodate both small and large quantities.
About DTG vs DTF Printing: Which printing Solution is better? You can read this post to learn more for your best choice of tshirt printing.
Comparison with Screen Printing
Is DTF better than screen printing? this post will give you an answer for the comparison of the two printing methods. DTF printing eliminates the need for screen stencils, making it a more efficient and cost-effective process.
Screen printing is better suited for large quantities and designs with fewer colors, while DTF printing allows for intricate and multicolor designs with ease.
DTF printing offers a higher level of detail and sharper edges compared to screen printing.
Comparison with Heat Transfer Printing
Let’s learn about the difference between DTF Print and T-shirt Heat Transfer Printing other customization methods, DTF printing does not require a transfer medium, making it a simpler and more streamlined process than heat transfer printing.
DTF printing offers better color vibrancy and durability compared to heat transfer printing.
Heat transfer printing is more suitable for single-color or simple designs, while DTF printing excels in reproducing complex and detailed designs.
In conclusion, DTF printing offers a unique and efficient method for achieving vibrant and durable prints on various fabric types. With its versatility, high-quality results, and cost-effectiveness, DTF printing has become a popular choice for individuals and businesses looking to add a personal touch to their products.
DTF printing has revolutionized the printing industry, offering a direct and efficient method for creating vibrant and durable prints on a wide range of fabrics. In this comprehensive guide, we explored the process of DTF printing, from understanding its advantages and differences from other printing methods to providing step-by-step instructions for achieving successful prints.
By following the outlined guidelines and considering the troubleshooting tips and maintenance suggestions, you’ll be well-equipped to embark on your DTF printing journey. Remember to experiment, practice, and refine your techniques to achieve the best results.
If you’re already familiar with heat transfer printing, DTF is the perfect complementary technique to increase your performance and make your business even more profitable.
So why wait? Unlock the potential of DTF printing and elevate your printing capabilities today!
And don’t hesitate to contact us if you have any further questions about T-shirt personalisation and DTF printing. Remember that you can subscribe to our Youtube channel and to our BLOG to keep up to date with the latest news and other interesting information about the world of personalisation.
FAQs
Frequently encountered problems in dtf printing:
Is DTF printing suitable for all fabric types?
DTF printing works well on various fabric types, including cotton, polyester, and blends. However, the composition and texture of the fabric can affect the quality of the prints. Smooth and flat fabrics tend to yield the best results.
Can I use DTF printing for dark-colored fabrics?
Yes, DTF printing is compatible with both light and dark-colored fabrics. For dark-colored fabrics, an additional layer of white ink is often necessary to enhance color vibrancy.
How durable are DTF prints?
DTF prints are highly durable and can withstand multiple washes without fading or cracking. Proper curing during the printing process ensures maximum durability.
Do I need specialized equipment for DTF printing?
Yes, DTF printing requires specialized equipment, including a DTF printer, heat press, and Powder Shaker and Dryer machine. These tools are designed specifically for the DTF printing process.
Can I achieve detailed prints with DTF printing?
Absolutely! DTF printing allows for high levels of detail and sharpness, making it ideal for reproducing intricate designs with precision.