Sublimation Paper Manufacturing Process
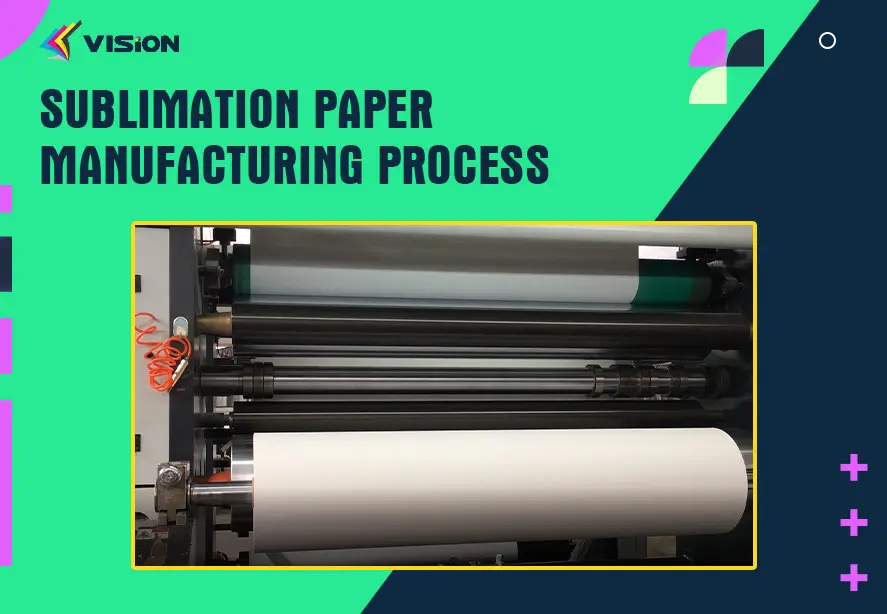
Sublimation printing is a fantastic way to achieve vibrant, durable prints on various materials. A crucial component of this process is sublimation paper, the medium that holds the design before it’s transferred onto the final substrate. But have you ever wondered how sublimation paper is made? Let’s take a journey behind the scenes to explore the intricate manufacturing process of sublimation paper.
What is Sublimation Paper?
Sublimation paper is a specialized paper designed to hold and release sublimation inks when heat and pressure are applied. It’s engineered to perform a critical role in sublimation printing, ensuring that the inks transfer smoothly and accurately onto the desired material.
Key Properties and Characteristics
Sublimation paper must have several key properties:
High ink absorption: To hold the sublimation inks without bleeding.
Quick drying: To allow handling without smudging.
High release efficiency: To ensure maximum ink transfer during the sublimation process.
Heat resistance: To withstand the high temperatures used in sublimation.
Raw Materials for Sublimation Paper
The production of sublimation paper starts with the selection of high-quality raw materials.
Types of Base Paper
The base paper used in sublimation paper manufacturing is typically made from high-grade cellulose fibers, which provide the necessary strength and durability.
Special Coatings and Their Roles
The key to sublimation paper’s performance is its special coating. This coating is formulated to hold the ink until it is transferred during the sublimation process. It often includes substances that enhance ink absorption and release.
The Manufacturing Process: Step-by-Step
The creation of sublimation paper involves several precise steps, each crucial to ensuring the paper’s quality and performance.
Pulping and Base Paper Production
The process begins with the preparation of pulp from cellulose fibers. The pulp is then formed into sheets of paper through pressing and drying.
Coating Application
The dried base paper is coated with a special layer designed to hold sublimation inks. This coating can be applied using various methods, such as roller coating or spraying.
Drying and Curing
Once coated, the paper must be dried and cured to ensure the coating is stable and performs correctly during printing.
Pulping and Base Paper Production
Source and Preparation of Pulp
The pulp used in sublimation paper is typically sourced from sustainably managed forests. The cellulose fibers are processed to remove impurities and achieve the desired consistency.
Paper Formation and Pressing
The prepared pulp is spread into thin layers and pressed to remove excess water, forming sheets of base paper. These sheets are then dried to create a stable foundation for the sublimation coating.
Sublimation paper manufacturing supplier
Coating Application
Types of Coatings Used
The coatings applied to sublimation paper can vary but generally include a mix of binders and additives that enhance ink absorption and release properties.
Application Methods
Coatings are applied using methods such as roller coating, which ensures an even distribution of the coating material across the paper’s surface.
Ensuring Uniformity and Consistency
To ensure high performance, the coating process must be carefully controlled to maintain uniformity and consistency across the entire surface of the paper.
Drying and Curing
Drying Techniques
After coating, the paper is passed through drying units to remove any remaining moisture. This step is crucial to prevent smudging and ensure the paper is ready for use.
Curing for Stability and Performance
Curing involves exposing the coated paper to controlled heat, which stabilizes the coating and enhances its performance during sublimation.
Quality Control in Manufacturing
Importance of Quality Checks
Quality control is essential in sublimation paper manufacturing to ensure that each batch meets the required standards for performance.
Common Quality Control Methods
Methods include visual inspections, measurements of coating thickness, and testing the paper’s ink absorption and release properties.
Environmental Considerations
Sustainability in Raw Materials
Sublimation paper manufacturers are increasingly focusing on using raw materials from sustainable sources to reduce the environmental impact.
Eco-Friendly Production Practices
Efforts include minimizing waste, recycling water used in the process, and reducing the use of harmful chemicals.
Challenges in Sublimation Paper Manufacturing
Common Issues and Their Solutions
Challenges such as inconsistent coating or insufficient drying can affect the paper’s performance. Sublimation paper manufacturers use advanced technologies and strict quality control to address these issues.
Technological Advancements
Innovations in coating formulations and application methods continue to improve the quality and consistency of sublimation paper.
Innovations in Sublimation Paper Technology
Recent Advancements
Recent advancements include the development of faster-drying coatings and papers that offer improved ink release efficiency.
Future Trends
Future trends may involve even more sustainable production methods and the creation of sublimation papers tailored for specific applications.
Understanding the manufacturing process of sublimation paper highlights the complexity and precision involved in creating this essential component of sublimation printing. From the selection of raw materials to the final quality checks, each step is crucial in ensuring the paper performs perfectly during the printing process. High-quality sublimation paper is key to achieving vibrant, durable prints, making it an indispensable tool for anyone involved in sublimation printing.
Related:
Our 4 Best Sublimation Paper Types – Which One is best for You
What is best way to keep sublimation paper?