Attentions for Self-Weeding (no-cut ) laser dark transfer paper
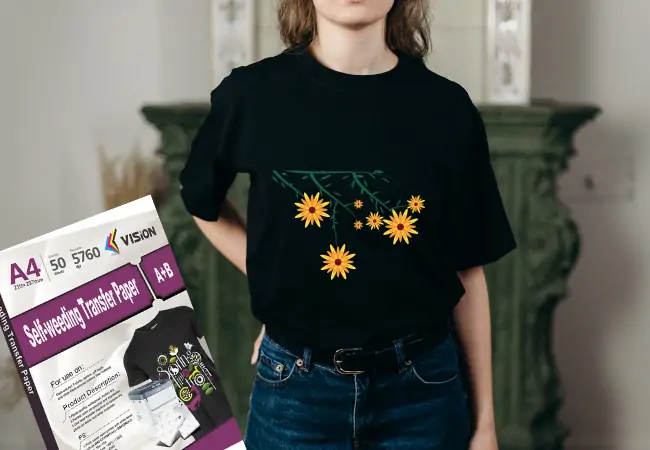
Some customers often encounter some operational problems when using our self-weeding transfer paper, which leads to transfer failure or unsatisfactory results. Now we summarize what should be paid attention to when using this heat transfer paper.
1. Press down the heat press board before transfer printing, let the silicone pad below be fully heated; put the printed pattern face to the silicone pad, and bake for 1-2min to increase the success rate of transfer printing.
2. If there are white parts in the pattern, you need to use OKI C711WT. If there is no white part, you can choose OKI or other printers, which are limited to color laser printers (other types of printers print patterns, and the transfer success rate is much lower, so it is not recommended to use ).
3. The format of the picture needs to be a vector file in CDR\EPS format. This is very important. It is difficult to transfer pictures in other formats.
4. The temperature and time of transfer printing need to be adjusted according to the different needs of the heat press machine. The recommended temperature is 160-170 ?, and the transfer time is 60-90 seconds. If the pattern is small and simple, the transfer time can be reduced by 60 seconds. If the pattern is large , Complicated, the time takes 90 seconds; the transfer temperature should not be too high, if the temperature is too high, it will destroy the coating structure on the transfer paper, the coating will soften, and the A film cannot be completely hollowed out when the B paper is torn off The pattern will cause the pattern to be transferred to B paper, and the transfer will fail.
5. When the B paper hollows out the A film pattern, the A film is on the bottom with the pattern facing up, and the B paper is on the upper transfer side to cover the A film. Do not leak the pattern part. If A is on the top, you can only tear off A when hollowing out, which will cause A There will be curls, and it will be difficult to place and align during the second step of transferring the fabric.
6. After the heat press machine pops up, smooth the B paper with both hands, wait for 8-10 seconds, and then heat the B paper. The transfer paper for shirts cannot leave the ironing board. Pausing will result in a noticeable imprint on the pattern.
7. In the process of tearing off the B paper, it is not allowed to cool down the transfer paper quickly. Rapid cooling will cause the transfer to fail.
8. After the A film is transferred to the fabric, after the heat press machine bounces up, take the fabric away from the heat press board evenly. During the process of taking it off, prevent the A film from warping, which will cause the pattern to not be transferred to the fabric.
9. When tearing off the A film, you must wait until the fabric is completely cooled. During the cooling process, do not perform other operations on the fabric. Place it still and let it cool naturally.
10. In order to ensure a good transfer effect, the speed of tearing off the A film should be slow, not too fast, and the pattern will be damaged if it is too fast.
11. Try to lower the angle between the torn A film and the fabric, and lower the angle between the torn A film and the fabric, the smaller the better.
12. After tearing off the A film, under the same temperature and pressure time, press the transferred pattern for 3-5 seconds to increase the firmness of the pattern. The pattern that has not been pressed again, when washing will cause the pattern to fall off.
13. The transfer fabric needs to be pure cotton fabric. It is recommended to choose the fabric with low elasticity and relatively rough fabric surface. The fabric pattern with high elasticity and smooth surface has relatively low adhesion. It is difficult to tear off the A film after the transfer fabric is applied. , greatly reducing the success rate of transfer.
14. Since the pattern is made of toner, stretching the fabric will cause the pattern to break, so the fabric cannot be pulled vigorously; when washing, do not directly rub the pattern, do not bleach, do not soak for a long time, and do not dry Dry.
If you encounter any problems when using our digital printing products by VISION factory, you can contact us at any time, we will help you solve them as soon as possible.