Top Tips for Vibrant Colors in DTF Printing
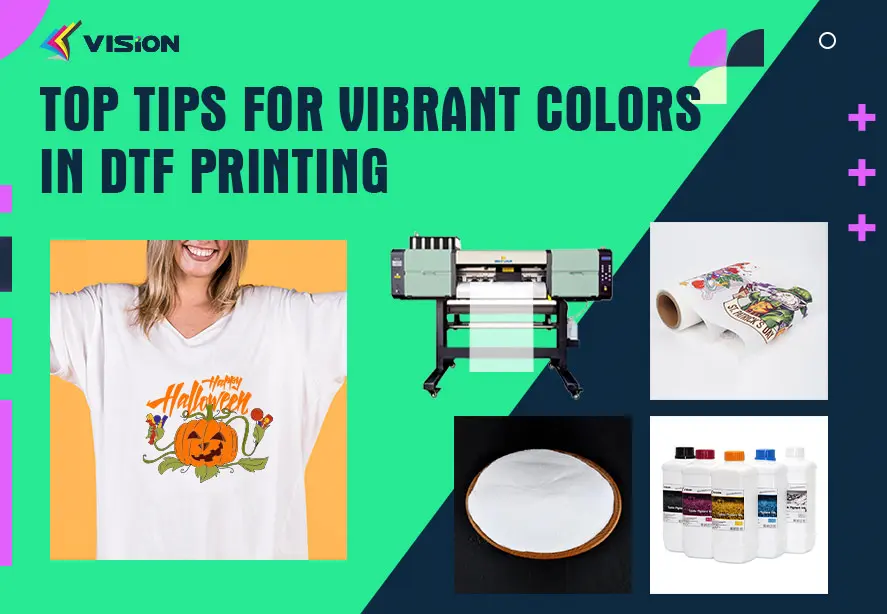
Achieving vivid and vibrant colors in DTF printing requires a combination of precision, the right materials, and a keen understanding of the printing process. Whether you’re creating custom apparel or promotional items, vibrant prints can significantly enhance the product’s appeal. Here, we outline the most effective methods and techniques to ensure your DTF prints stand out with exceptional color brilliance.
10 Tips for Vibrant Colors in DTF Printing
1. Use High-Quality DTF Inks
The foundation of any vibrant DTF print lies in the quality of the inks used. High-quality inks provide richer, more saturated colors that pop on the final product.
Pigment Density: Opt for inks with a high pigment density to ensure colors remain bold and do not fade quickly.
Color Gamut: Ensure the inks offer a wide color gamut for accurate color reproduction.
Brand Consistency: Stick with reputable brands known for their consistency and quality, such as VISION dtf inks.
Investing in premium inks can significantly reduce issues like banding, fading, and color inconsistencies.
2. Choose the Right Film
The DTF transfer film plays a crucial role in determining color vibrancy. Select films that are specifically designed to enhance ink adhesion and color depth.
Matte vs. Glossy: Matte films provide a soft finish, while glossy films offer a more reflective, saturated appearance.
Thickness: Use films with a standard thickness of 75 to 100 microns to achieve optimal ink absorption.
Compatibility: Ensure the film is compatible with your printer and ink type to avoid color distortion.
Look for cold peel or hot peel films based on your preference for workflow and finish quality.
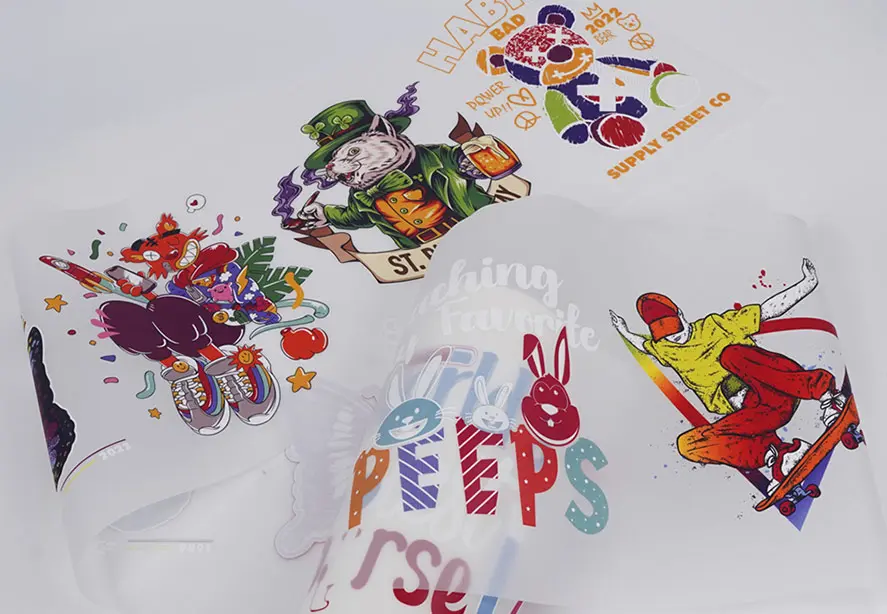
dtf transfer film
3. Optimize Printer Settings
Maximizing the performance of your DTF printer involves fine-tuning the settings to achieve the best color output.
Resolution: Use a resolution of at least 1440 DPI for crisp and detailed prints.
Ink Saturation: Adjust ink saturation settings to avoid under-saturation or over-saturation. A balance ensures colors are bright but not bleeding.
White Underbase: Apply a solid white underbase beneath the colors to enhance vibrancy on dark garments.
Test different configurations to identify the optimal settings for your specific printer model.
4. Use a High-Quality Adhesive Powder
The adhesive powder used in the DTF process impacts both the durability and color brilliance of the print.
Fine Grain Powder: Opt for a fine-grain adhesive powder for smoother coverage and better adherence.
Application Uniformity: Ensure the powder is evenly applied to avoid blotchy areas that can affect color integrity.
Curing Temperature: Cure the adhesive powder at the correct temperature (typically between 150°C to 160°C) to achieve a durable bond without burning the colors.
Properly cured adhesive ensures the print remains vibrant after multiple washes.
5. Maintain Accurate Color Profiles
Using the correct ICC color profiles ensures that the colors displayed on the screen match the final printed output.
Custom Profiles: Create custom ICC profiles tailored to your printer, inks, and film.
Regular Calibration: Calibrate your printer regularly to maintain consistent color accuracy.
Software Compatibility: Use high-quality RIP (Raster Image Processor) software, such as Kothari RIP or CADlink, to control color output precisely.
Accurate color profiling minimizes discrepancies and ensures reliable, vibrant results.
6. Pre-Treat Garments Properly
Proper preparation of garments before printing can significantly enhance color vibrancy and durability.
Clean Surface: Ensure the garment surface is clean and free of dust or contaminants.
Pre-Pressing: Pre-press the garment at 160°C for 5 to 10 seconds to remove moisture and flatten the fabric.
Fabric Type: Use materials like 100% cotton, polyester blends, or synthetic fabrics that are known for their print-friendly properties.
A properly prepared garment ensures the DTF transfer adheres uniformly, preserving color brightness.
7. Ensure Proper Curing of the Ink
The curing process solidifies the ink and ensures it maintains its vibrancy over time.
Curing Temperature: Cure the print at the recommended temperature, typically 160°C for 2 to 3 minutes.
Heat Press Pressure: Apply even pressure during the curing process to avoid uneven color distribution.
Check for Overheating: Over-curing can dull colors, while under-curing can lead to poor wash durability.
A correctly cured print will exhibit long-lasting, vibrant colors that endure repeated use and washing.
How to use DTF transfer film for your tshirt business?
8. Store Materials Correctly
Proper storage of DTF materials preserves their quality and ensures consistent print results.
Ink Storage: Store inks in a cool, dark environment to prevent them from degrading.
Film Protection: Keep films in a sealed package to protect them from humidity and contaminants.
Powder Storage: Store adhesive powders in airtight containers to prevent clumping.
Maintaining the integrity of your materials helps avoid color inconsistencies during printing.
Regular maintenance of your DTF printer is essential for producing consistently vibrant prints.
Clean Print Heads: Perform regular print head cleanings to prevent clogs and ensure smooth ink flow.
Check Ink Lines: Inspect ink lines for air bubbles or blockages that can affect color output.
Firmware Updates: Keep your printer firmware up to date for optimal performance and color accuracy.
A well-maintained printer delivers sharper, more vibrant prints and reduces downtime.
10. Test and Adjust Frequently
Continuous testing and adjustments are key to achieving the most vibrant DTF prints possible.
Print Samples: Regularly print test samples to gauge color accuracy and vibrancy.
Feedback Loop: Adjust printer settings, ink volumes, and curing times based on the results.
Document Settings: Keep a log of successful settings to streamline future projects.
Testing ensures that you stay ahead of any potential issues and consistently produce high-quality, vibrant prints.
Achieving vibrant colors in DTF printing involves a blend of the right materials, precise settings, and meticulous techniques. By focusing on high-quality inks, optimal printer settings, accurate color profiles, and proper garment preparation, you can ensure your prints stand out with exceptional brightness and durability. Regular maintenance and continual testing will keep your process refined and your prints consistently stunning.
Related:
Can you use DTF film without adhesive powder?
Do you need special ink for DTF transfers?
Unveiling High-Quality DTF Film
Troubleshooting Common DTF Printing Issues
Choosing the Best DTF Printers For Your Business in 2024